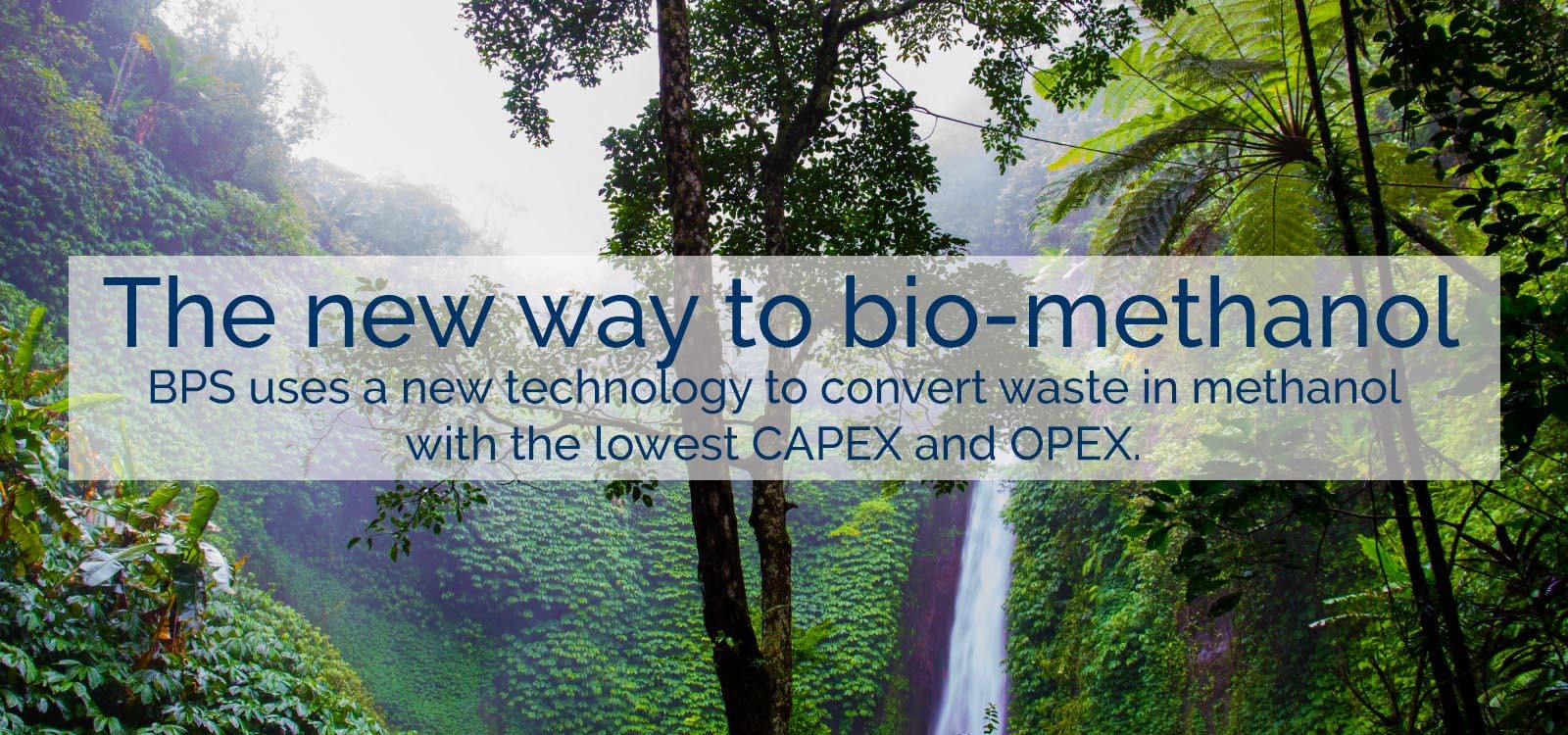
Capacity of the Bio-Methanol plant verses logistic and economic issues
The basic design of BPS to produce 2.5 ton/hr methanol is based on logistic and economic criteria. In principal the basic design can be multiplied or divided by a factor of 3 to 4, as common in chemical engineering.
The economical reason to produce 2.5 ton/hr has its origin in the added value between feedstock and methanol produced related to the CAPEX. This is a choice of a moment some time ago. Related to the price set at a that time. And related to Return on Investments at that time. But time changes and so does these expectations of ROI and price set of feedstock and methanol. For skid mounted design though 2.5 ton/hr is the optimal design capacity. If we stick to a skid mounted design multiples of 2.5 ton/hr can be easily created by parallel production streams for higher capacities. But of course also another way is to have a fixed installation at a certain place at any production level between 1 and 10 ton/hr based on the present basic design.
Another consideration may be if Bio-Methanol is a key issue in a market approach because it is bio. And at this time there is not any sustainable delivery of bio-methanol is possible. The expected consumption of bio-methanol may in such case also be the lead factor for choosing the right production capacity. In that case G1 may even be a better choice than G2 biomass. So there are many criteria for choosing the right production capacity and feedstock based on economic evaluations.
Logistic reasons also debit to the choice of the production capacity of 2.5 ton/hr methanol. As the target of the installation is to produce the methanol out of G2 biomass, we considered the logistic of the acquisition of this biomass in a special region. Even in tropical areas, as analyzed in the business plan, the installation can hardly run 24/7 during a year. As the distance to the biomass, which is of low density and high water content, gets too far of the installation to be effective. Therefore the choice is made to design the installation skid mounted. And the installation can be moved to the biomass rather than that the biomass is moved over long distances to the installation. Also here this is an assumption. If the biomass is concentrated at a certain place, as is the case by sugar cane, or 24/7 is an option for another reason, other design capacities than 2.5 ton/hr may be advantageous in the same way as described above.